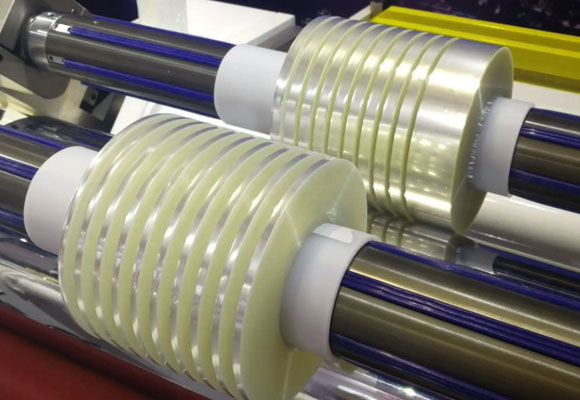
Types of Slitting Explained
In the converting industry, one of the most important processes during production is slitting. Slitting refers to converting large, heavy rolls of soft and flexible materials, such as film, foil, plastics, technical textiles, and paper, into narrower strips for further processing. A slitting machine or slitter is used to create nice and clean cuts and finish the slitting job. Since accurately and precisely slitting soft materials is challenging, it is vital to choose the right type of slitting as well as proper slitting blades. Konetool is an experienced supplier of tungsten carbide slitting blades. Today, we will share our practical experience in slitting and explain the definition, machine, types of slitting, and slitting blades that are mounted on the slitting machines.
What is slitting in converting?
When it comes to converting, slitting is too familiar to everyone in this industry. Why is slitting so crucial? These flexible materials are initially manufactured into heavy and large rolls for easy shipping and storage, which are also called parent rolls or master rolls. Parent rolls need to be cut into small sizes to meet production requirements. Slitting is a perfect method to finish the task. Through slitting, master rolls are converted into small and narrower strips.
Slitting is suitable for processing a wide range of soft materials, including paper, films, foils, fabrics, textiles, leathers, vinyl, plastics, tapes, and more. It is widely used in various industries, like packaging, automotive, food processing, medical, and recycling.
Types of slitting
Log slitting and rewind slitting are two important types of slitting. As the name implies, rewind slitting refers to unwinding the master rolls, slicing the unwound long sheets, and then rewinding the narrower rolls. Log slitting, however, is cutting the parent roll directly without the unwinding step. The following is a detailed explanation.
Log slitting
(Image Source: strouse.com)
To begin with, the operator loads a heavy, large roll of flexible material onto a log slitter. We call this wide roll a “log roll” because it looks like a large tree trunk. A log slitter is also called a “lathe slitter” or “baloney slicer” since its working method resembles a lathe. The log roll is loaded onto a spinning mandrel horizontally. Then, a circular blade starts slitting the roll into the required widths. This is the process of log slitting.
Log slitting is ideal for cutting different soft materials such as tapes, PVC, papers, foams, tissues, films, and foils.
Rewind slitting
There are three types of rewind slitting: razor slitting, shear slitting, and crush cutting.
A. Razor slitting
Razor slitting employs a sharp blade or multiple blades (called industrial razor blades) to cut the material. The blade is held by a blade holder to stay stationary on a slitting machine. When the material passes through the razor blade, the slitting job is done.
Type: Two types of razor slitting methods are frequently used that are razor-in-air and razor-in-groove. The blade is placed on top of the material without any support in the former method. In the latter, the blade is mounted at the bottom with a grooved roll supporting the slitting job. Razor-in-groove slitting requires a higher running speed than razor-in-air slitting.
Material: Best for thin, light, non-abrasive substrates, including thin films, light foils, tapes, plastics, vinyl, and ribbons.
Advantage: Economical, clean, easy to set up and maintain.
Disadvantage: Not suitable for cutting heavy, abrasive woven materials; Limited cutting speed; Generating more heat.
B. Shear slitting
The mechanism for shear slitting is like a pair of scissors which is quite simple to understand. Two circular knives move in a scissor action that is called “male knife” (top mounted) and “female knife” (bottom mounted). Correctly setting up the rotary knives to create an appropriate nip point is crucial, or the blades will easily wear.
Material: Best for thick films, foils, metal sheets, laminates, and composites.
Advantage: Accurate and precise cuts; Relatively high speed; Generating less heat and dust.
Disadvantage: Expensive, difficult to set up.
C. Crush cutting
Crush cutting, or score slitting, is a traditional slitting method and is the most frequently used. It can deal with materials of various thicknesses and hardness. The parent roll is loaded onto a rotating anvil roll or crush roll, and a rotating circular knife (or multiple knives) is pressed against the roll to cut the material.
Material: Best for pressure-sensitive adhesives, tough and thick non-wovens, laminates, tapes, rubber, fabrics, and more.
Advantage: Economical, easy to set up and maintain.
Disadvantage: Low-quality and less precise cuts; Limited cutting speed; Generating more dust.
Factors to consider when selecting slitting methods
Material being cut is the most important factor to consider. For example, if you are going to slit thin substrates, use razor slitting. Thick and pressure-sensitive materials should be processed through crush cutting.
Besides, do you work with professional converters? Log slitting, razor slitting, and crush cutting are easy to set up and maintain. However, shear slitting is difficult to set up and requires more professional knowledge.
The slitting results are also significant. Shear slitting creates more accurate and smoother cuts compared to other slitting types.
Another factor is the runtime. If the runtime of your machine is very long, use shear slitting because it creates less heat and dust.
Last but not least, your budget. Shear slitting is more expensive than other types of slitting. Therefore, you should select a slitting type that is under your project budget.
Slitting blades
Employing the right slitting blade can improve the efficiency and performance of the slitting job. Konetool supplies a wide range of outperformed tungsten carbide slitting blades, including industrial razor blades, Zund blades, dished knives, and more. Request a quote today to get further information about our slitting knives!