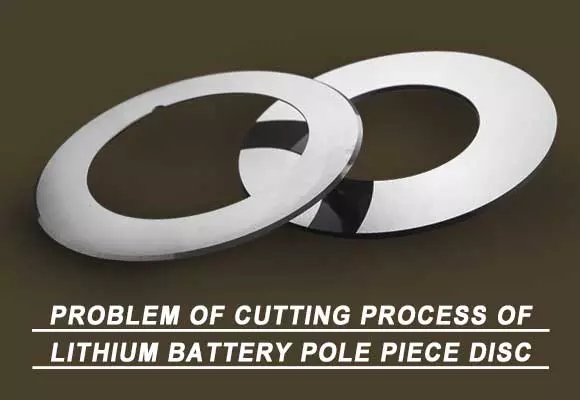
Problems of Cutting Process of Lithium Battery Pole Piece Disc
High-precision tungsten carbide slitting knives are key products specially developed and produced by the battery industry for higher requirements for incisions. They have good wear resistance and high processing accuracy. Tool outer circle precision is high, and the cutting edge is strictly enlarged and tested. Service life is long. It is an ideal tool for users in the battery industry to reduce cutting costs and improve cutting quality.
In the pole piece slitting process, the lateral pressure and overlap of the cutter are the main adjustment parameters of the disc cutter section, which need to be adjusted in detail according to the nature and thickness of the pole piece. In the past equipment manufacturing and technology, the adjustment of the knife often lacks accurate numerical parameters but is based on experience to make corresponding adjustments according to the batch of pole pieces. With the advancement of equipment technology, tool adjustment technology has also been continuously improved and digitized. Nowadays, a pole piece slitting machine tool lateral pressure cylinder automatic adjustment device appears. During pole piece slitting, the side pressure of the cutter is adjusted by setting the cylinder pressure to control the cutting quality.

The main defects of pole piece slitting
The main particles of the coating on the fracture surface peeled and fractured, and the current collector was plastically cut and torn. When the compaction density of the pole piece coating increases and the binding force between the particles increases, some particles of the pole piece coating also appears to be cut off. The main defects in pole piece slitting include the following:
(1) Burr
Burrs, especially metal burrs, are extremely harmful to lithium batteries. Larger metal burrs directly pierce the separator and cause a short circuit between the positive and negative electrodes. The pole piece slitting process is the main process of burrs in the lithium-ion battery manufacturing process. In order to avoid this situation, it is most important to find the most suitable lateral pressure and tool overlap according to the nature and thickness of the pole piece when adjusting the knife. In addition, the edge quality of the pole piece can be improved by cutting knife chamfering and winding tension.
(2) Wave edge
There are material dropouts, wavy edge defects, and wavy edges during pole piece cutting. When wavy edges appear, edge correction jitter will occur when the pole piece is slitting and winding, which will cause process accuracy and adversely affect the final thickness and shape of the battery.
(3) Drop powder
The powder drop of the pole pieces will affect the battery performance. When the positive electrode drops powder, the battery capacity decreases, and when the negative electrode drops powder, the negative electrode cannot wrap the positive electrode, which is likely to cause lithium precipitation.

The above quality problems are mainly solved by finding suitable tool adjustment parameters.
The size does not meet the requirements
The pole piece slitting machine cuts the rolled battery pole pieces according to the battery specifications and requires high dimensional accuracy of the slitting pole pieces. When designing a wound battery, the separator should wrap the negative electrode to avoid direct contact between the positive and negative pole pieces to form a short circuit, and the negative electrode should wrap the positive electrode to avoid lithium ions in the positive electrode during charging. The size difference between the separator, the negative electrode, and the positive electrode is 2-3mm, and as the specific energy requirement increases, the size difference is continuously reduced. Therefore, the dimensional accuracy of the pole piece is required to be higher and higher, otherwise, the battery will have serious quality problems.

In addition to hard alloy lithium battery slitter blades, KONETOOL also produces various specifications of high-precision tungsten steel slitting circular knives, which are widely used in electronic industry such as copper and aluminum and other non-ferrous metal materials and silicon steel sheets, ordinary steel sheets, and packaging industry materials High-precision slitting. You can consult us at any time if you have any questions during the purchase or use process.