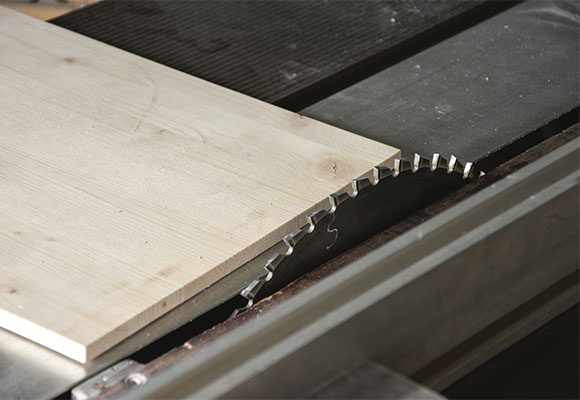
How To Choose Woodworking Circular Saw Blades?
When choosing circular saw blades for your woodworking projects, there are a number of aspects that should be considered. For example, type, thickness, cutting speed, cutting direction, feeding speed, etc. Those things are attributed to the selection of parameters like tooth configuration and angle of carbide circular saw blade for cutting tool ultimately. The selection of woodworking circular saw blades is briefly introduced below.

Firstly, Tooth Configuration
There are several types of tooth configurations for circular saw blades, including Alternate top bevels (ATB), Triple-chip grind (TCG), flat teeth (FZ), etc. It is mainly based on the character of raw materials to be processed. ATB teeth are done for slitting and cross-cutting all kinds of soft, hard, and particleboard, it is equipped with anti-rebound protection teeth that are suitable for longitudinal cutting many types of materials. ATB saw blades with negative front angles are usually used for sawing veneers due to their sharp teeth and extraordinary quality.
Flat teeth are mainly applicated in processing common wood. The cost of this type is low, but the cutting edge is rough. A combination of trapezoidal teeth and flat teeth also can obtain higher sawing quality without grooving the saw blade, so veneer cracking will not occur during processing. It is fit for processing various double-faced wood-based panels.
Secondly, Tooth Angles
The angle parameter of the sawtooth part is complicated, choosing the angle parameter of the carbide circular saw blades correctly is of vital importance, it determines the quality of processing. The most important angle parameters are front angle, back angle, and wedge angle. The front angle mainly affects the force consumed by sawdust. The bigger the rake angle is, the better the cutting sharpness is, the lighter the processing is and the less effort is saved in pushing.
Generally, the selection of a carbide circular saw blade for the cutting tool is mainly related to the material of the workpiece. When the material of the workpiece is soft, a large front angle is recommended. Otherwise, the smaller angle is preferred.